Test Center
Increase the efficiency and quality of sorting processes with MEYER technology.
Welcome to the Meyer Test Center
Test your material samples
MEYER EUROPE invites current and future customers to conduct optical sorting tests on their own materials at our Test Center, located in Michałowice, near Warsaw. Thanks to its convenient location in central Poland, just 15 minutes from the international Chopin Airport, we offer easy access for customers from Poland and across Europe. Our qualified staff performs tests on materials provided by the customers, thoroughly explains the optical sorting process, showcases MEYER sorters, and helps tailor solutions that maximize the performance and efficiency of the entire sorting process.
Show me location of Test Center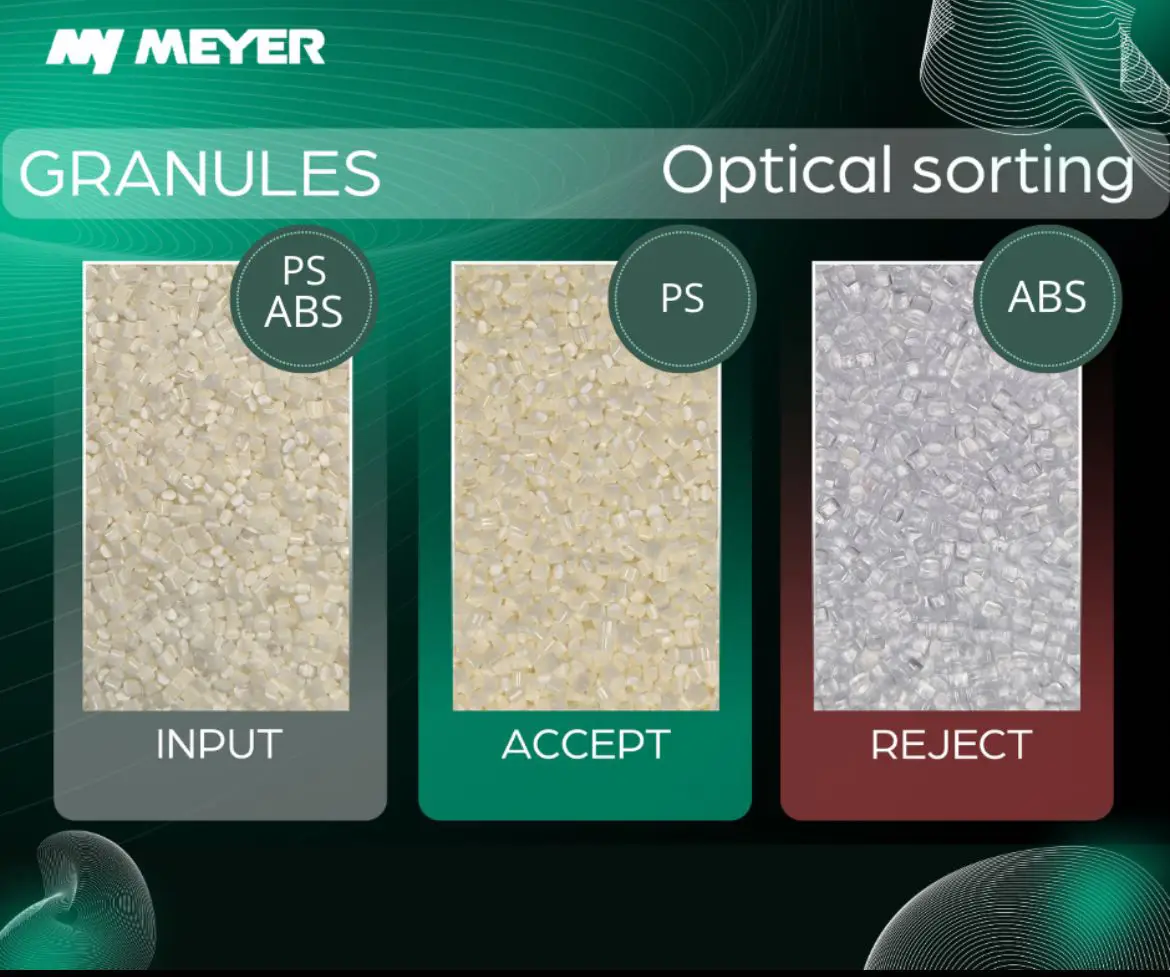
How can we help your business?
Recycling materials sorting
For the recycling industry, we offer color, polymer, and object sorters that enable sorting of materials such as plastics (including PET, HDPE, PP, PVC, etc.) based on differences in color, shape, and polymer composition. At our MEYER Europe Test Center, we conduct live tests to assess the effectiveness of optical sorting and customize solutions to meet each client's specific needs. Our specialists carry out a detailed analysis of the material, selecting the appropriate sorter configuration tailored to the individual requirements of the customer. Live tests allow clients to see how the sorting process works in practice, enabling better alignment of the solution with the production specifics. Through our services, we help improve the efficiency and quality of recycling processes, supporting the concept of a circular economy.
Schedule testsFood materials sorting
In our Test Center, we offer comprehensive optical sorting solutions for the food industry. We are equipped with color sorters and X-ray detectors, which allow for precise material separation based on color differences and the elimination of foreign objects such as glass, stones, or metals. Our equipment makes sorting lightweight materials like spices and teas, as well as heavier fractions like vegetables or frozen fruits, simpler and more efficient. During the tests, we thoroughly analyze each material and tailor the solution to its specific characteristics, ensuring the highest quality and process efficiency.
Schedule testsAgriculture
We tailor optical sorting solutions to the needs of the agricultural industry, offering machines for sorting seed materials, cereals, grains, beans, rice, seeds, and other agricultural products. Our sorters utilize color separation technology and InGaAs cameras that analyze grain density, enabling the effective removal of internally damaged fractions. Additionally, we offer X-ray detectors that serve as the final quality control point on the production line, eliminating foreign objects such as metals, glass, and stones. With our solutions, agricultural materials are prepared for further processing or sale, ensuring the highest quality and process efficiency. We support agriculture by providing innovative technologies that improve crop quality and production efficiency.
Schedule testsHow it works?
Send Us inquiry
Contact our representative to discuss the goals you aim to achieve with optical sorting solutions. Share detailed information about the materials you plan to sort and the results you wish to achieve, such as improving purity, increasing efficiency, and eliminating specific fractions.
Material shipment
Send material samples to our Test Center according to the guidelines provided by our representative (the size and type of sample depend on the material being sorted). Additionally, we recommend sending a bag of cleaned material, which represents the desired outcome of the sorting process, and separately packaging the defects that are to be removed during sorting.
Solution development
Our team of experts will develop tailored optical sorting solutions specifically for your materials. We will create the optimal configuration of equipment based on your requirements for cleanliness, efficiency, and the installation conditions in your facility. During live testing, you'll have the opportunity to see firsthand how the entire process works, from material analysis to the development of a comprehensive solution that perfectly fits your production needs.
Test results & sorting solutions
After conducting the tests, we will prepare a detailed report of the sorting process and its results. The report will include photo and video documentation, as well as samples from different stages of the sorting process, allowing you to review the results on actual material. Additionally, our team will work closely with you to develop the optimal solution for installing the optical sorter on your production line. We will ensure the proper preparation of the material for sorting and provide support during the installation preparations, ensuring the entire process runs smoothly and efficiently.
Why material testing is important?
Performance Verification
Conducting tests ensures that the optical sorting machine meets specific performance criteria and is capable of handling the materials as required. This verification helps avoid the risk of investing in equipment that may not meet operational needs.
Customization and Optimization
Material testing allows for the customization and optimization of the sorting machine according to the specific types of materials the customer needs to process. This ensures that the machine is tailored to the unique requirements of the business, improving sorting accuracy and efficiency.
Cost Savings
By testing materials beforehand, businesses can avoid the high costs associated with purchasing an unsuitable sorting solution. It helps identify the most cost-effective machine that delivers the desired results, thereby optimizing the investment and reducing unnecessary expenditure on future adjustments or replacements.
Technical Support and Education
During the testing phase, customers receive valuable support and education from the MEYER technical team. This includes explanations of the sorting process, assistance in understanding the machine’s functions, and advice on how to maximize its efficiency and effectiveness.
Proof of Concept
Material testing serves as a proof of concept, demonstrating that the sorting technology can handle the specific challenges presented by the customer’s materials. This can be especially important for businesses dealing with unique or challenging sorting requirements.
Risk Reduction
Testing materials with the sorting machine before purchase significantly reduces the business risk associated with new technology adoption. It provides a practical demonstration of how the machine works with the actual materials, thereby reducing uncertainties and potential operational risks.
Enhanced Recovery Rates
For recycling industries, testing helps in identifying the most efficient sorting solutions that can improve the recovery rates of recyclable materials, supporting sustainability goals and the principles of the Circular Economy.
Adaptability to Market Changes
Testing different materials allows businesses to adapt to market changes by understanding how different types of materials can be sorted and processed. This flexibility can be crucial in responding to shifts in supply, demand, and regulatory requirements.
Quality Assurance
Material testing helps ensure that the final sorted product will meet quality standards. This is particularly important in industries like food processing and recycling, where the purity and cleanliness of sorted materials are critical.
Every material is different. We will guide you
Every material for sorting has its unique characteristics and requirements that need a tailored approach to achieve the best sorting efficiency. Our experienced experts at MEYER fully understand this diversity and possess the knowledge to offer the most effective solutions tailored to your specific needs. With an in-depth understanding of various materials and advanced sorting technologies, we provide an effective and optimized sorting strategy, perfectly suited to the demands of your production.
Schedule testsYou can trust Our experts
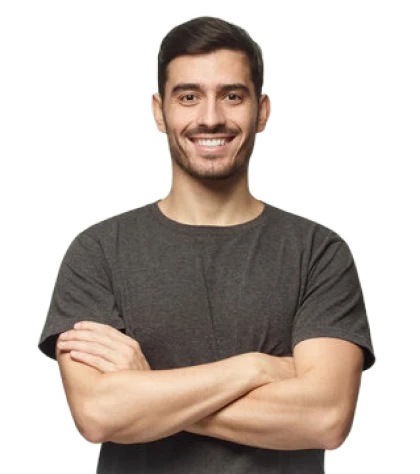
Marcel Rybiński
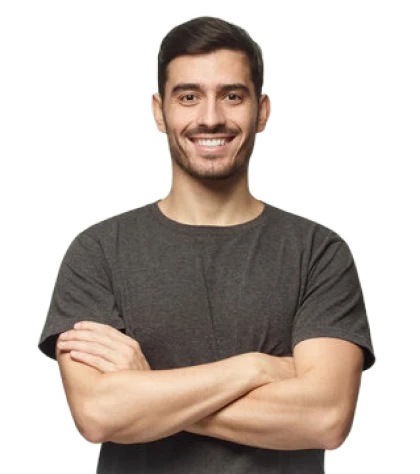
Marcel Rybiński
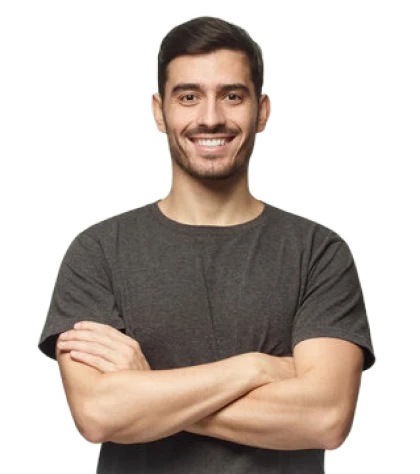
Marcel Rybiński
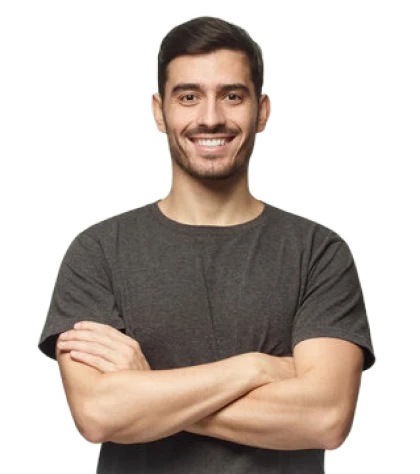
Marcel Rybiński
Schedule Your Optical Sorting Tests
Frequently Asked Questions
How can I schedule a test at Meyer Europe’s test center?
Contact the representative in your region or email us at sales@meyer-corp.eu. Our sales team will provide detailed instructions on how to prepare and send your materials to the test center.
Can I observe the testing process at Meyer Europe’s test center?
Yes, the entire process begins with sending us your material samples, followed by our service team developing the sorting solutions. Finally, we invite you to our test center, where you can observe the results of both our work and the sorter in action.
What is the typical turnaround time for test results at Meyer Europe’s test center?
The duration of the testing process depends on several factors, including the level of material contamination, sorting process expectations, and desired outcomes. Typically, preparing sorting solutions takes up to 2 weeks. After this period, our sales representative will either schedule a live testing date with you or send you sorting materials (videos, photos of the material, along with descriptions of the sorting stages and material samples).
Do I need to prepare my materials in any specific way before bringing them to the test center?
To achieve the best sorting results and receive the best solutions to your company’s needs, please prepare a sample of the standard material you wish to sort. It is recommended to prepare several material fractions, in the quantity depending on arrangements with our sales representative:
- Mixed Fraction: The standard material you want to sort.
- Accept Fraction: Showing the sorting effect you wish to achieve.
- Reject Fraction: A sample containing the contaminants you want to remove from your standard material.
Additionally, please provide a detailed description to our sales representative of your expectations and the fractions you want to separate during the sorting process.
This will ensure that the tests are conducted with the necessary precision and meet your company’s requirements. With a well-executed process, we can select the appropriate machines that meet your efficiency and material purity needs.
Can Meyer Europe’s test center assist with developing custom sorting solutions?
Yes, developing custom sorting solutions is a core part of our approach at Meyer Europe. We believe that the sale of every sorter should begin with testing, during which we create the solution that best fits the customer’s specific needs.